Nanoscale Multi-Metal 3D Printing for Voxel-by-Voxel Materials Design
Similar to salt in water or sugar in coffee, metals can be dissolved in liquid solvents. In contrast to dissolution of salt or sugar, dissolution of metals can be controlled using electric potentials. Researchers from three departments of ETH Zurich have now applied this approach to develop a new concept for nanoscale 3D printing of metals. Their work was recently described in Nature Communications.
“We force the dissolution of pure metals inside our print head and use the dissolved atoms as precursors for printing metals with a resolution better than 100 nm”, explains Alain Reiser, a doctoral student at the Department of Materials and lead author of the study. This simple and low-cost approach to nanoprinting avoids the use of nanoparticle inks and guarantees materials properties that can compete with the state-of-the-art microfabrication – a crucial step for the implementation of additive techniques in small-scale fabrication.
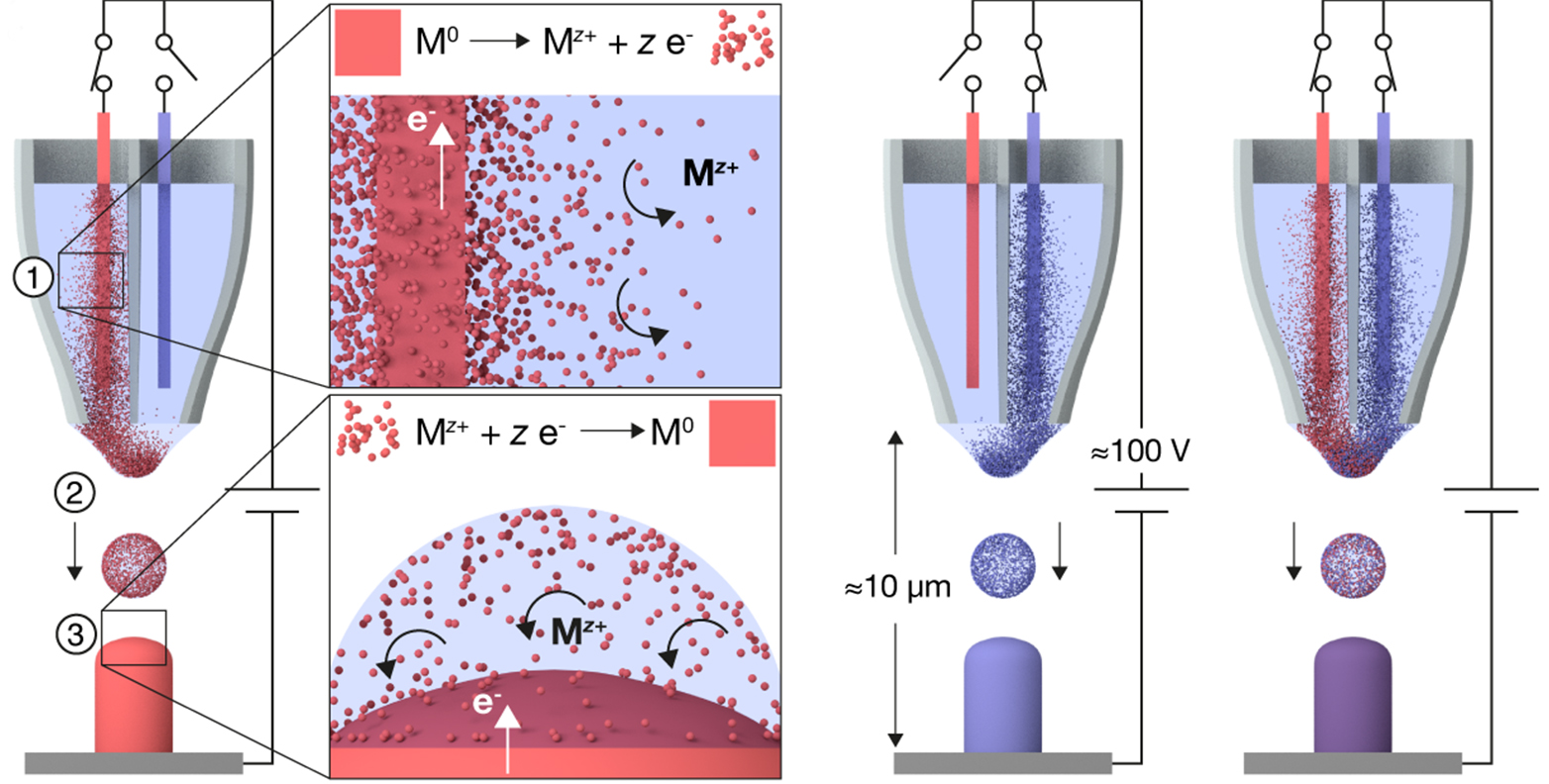
“Electrospraying has been used for mass spectrometry for more than 30 years, but one usually tries to avoid higher concentrations of metal salts”, says Renato Zenobi, a Professor at the Department of Chemistry and co-author of the study. “Here, we demonstrate that spraying metal ions can be exploited for the additive materials synthesis at the nanoscale.”
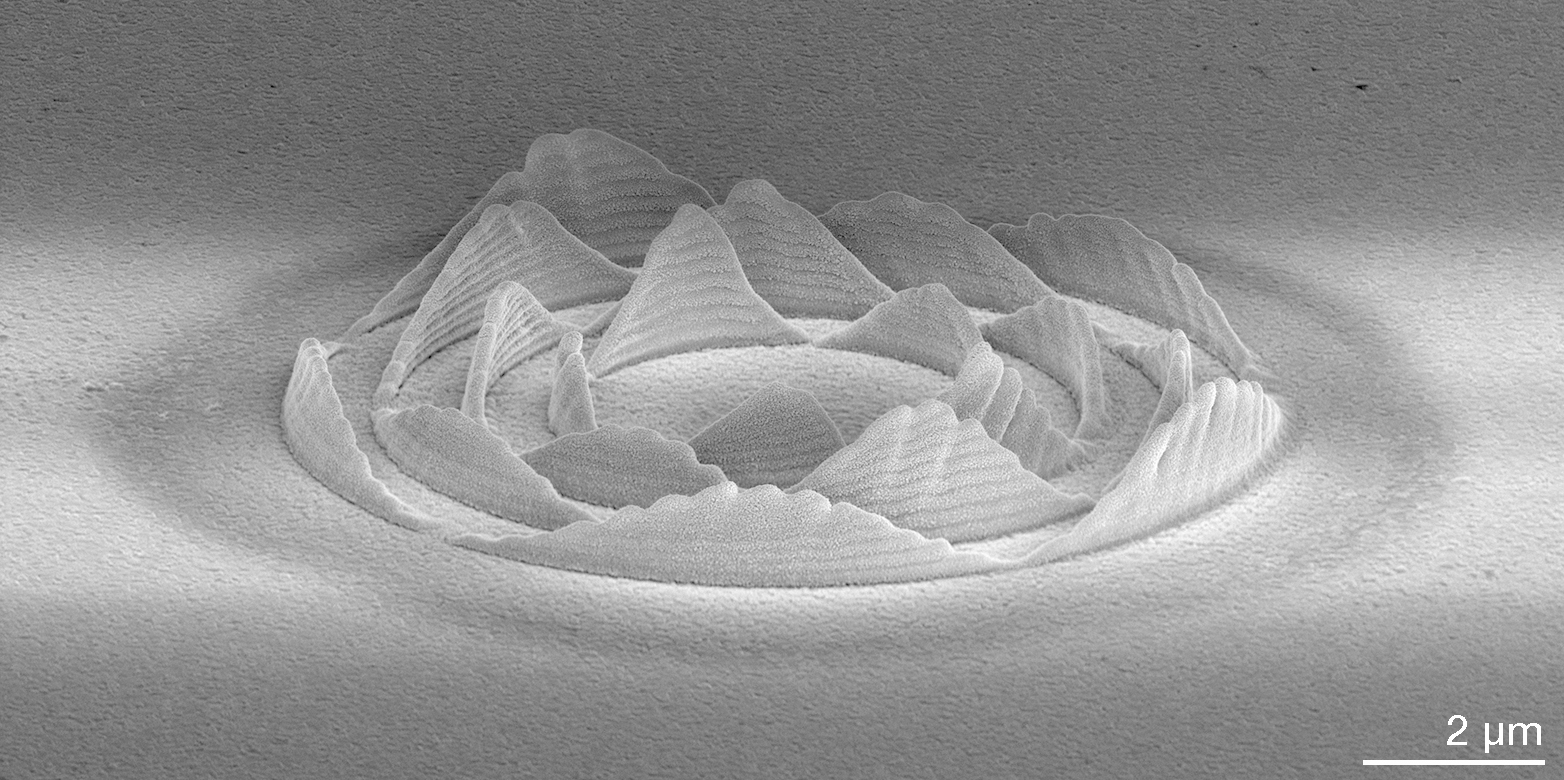
Multi-Material Printing with a Flick of a Finger
Avoiding inks has a further benefit: metals to be printed from a single nozzle can be switched on the mere flick of a switch. The technique enables alteration between two metals at a frequency of up to 10 Hz, facilitating multi-material printing with previously unseen detail. Prof. Dimos Poulikakos from the Department of Department of Mechanical and Process Engineering, who co-authored the study: "If you wanted to print two materials, the standard process was to use two separate print nozzles, each filled with the respective ink. This caused difficulties with alignment between the materials, and mixing the two materials was not possible at small scales. In contrast, our new approach enables easy tuning of the printed composition on the fly."
As different metals offer different properties, mixing two metals facilitates printing nanostructures with combined properties. Prof. Ralph Spolenak from the Department of Materials, whose lab led the study, is excited about the new possibilities that the technique offers: "The method offers great materials properties when printing single materials, but what is more exciting is the possibility to tune the printed composition during printing. Such control enables the manufacturing of 3D gradient materials with unprecedented spatial resolution. In the current study, we were able to show that we can tune the local porosity and thus the stiffness of printed nanowires or use less noble metals as sacrificial layers to easily print overhanging features.”
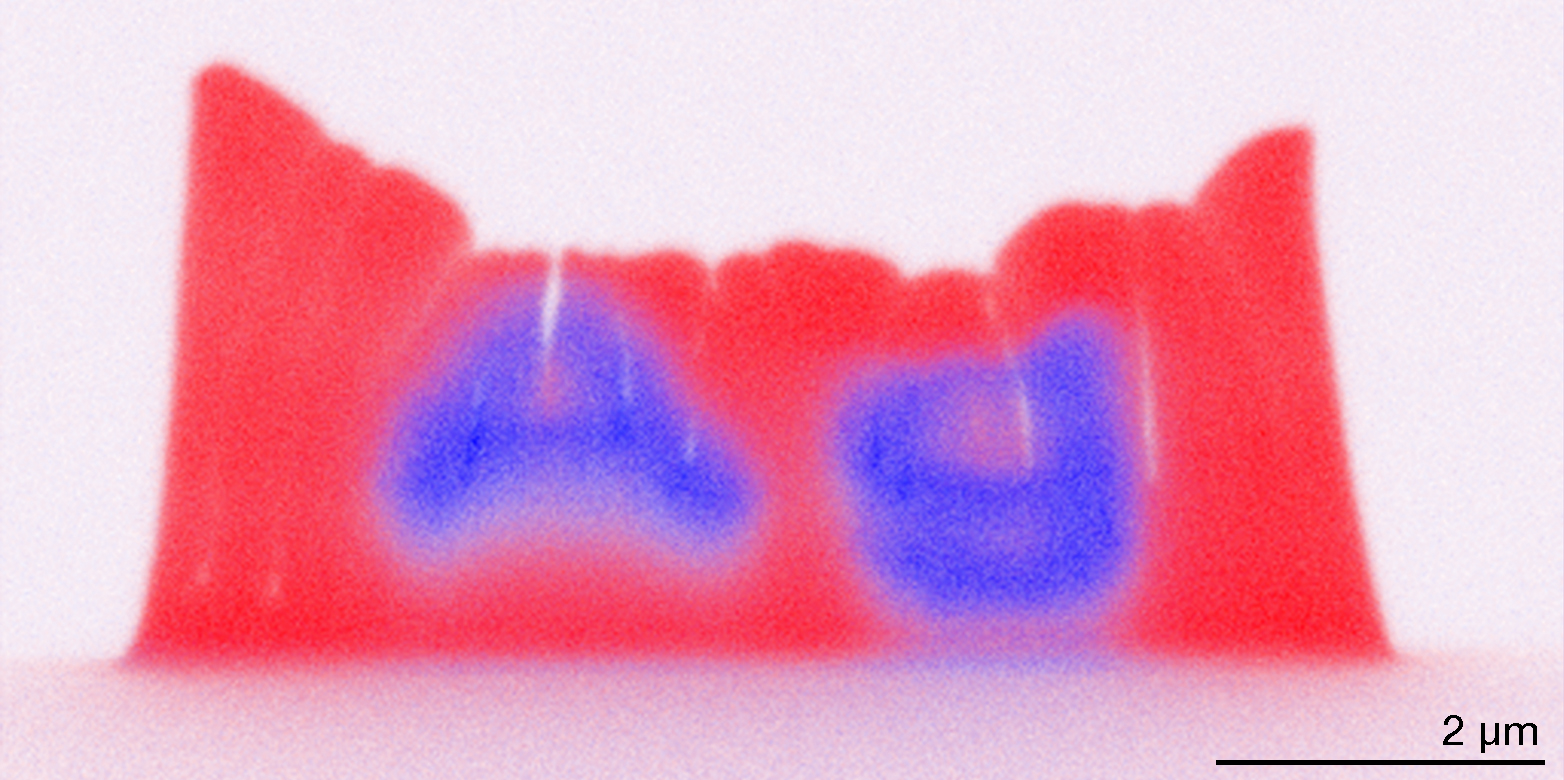
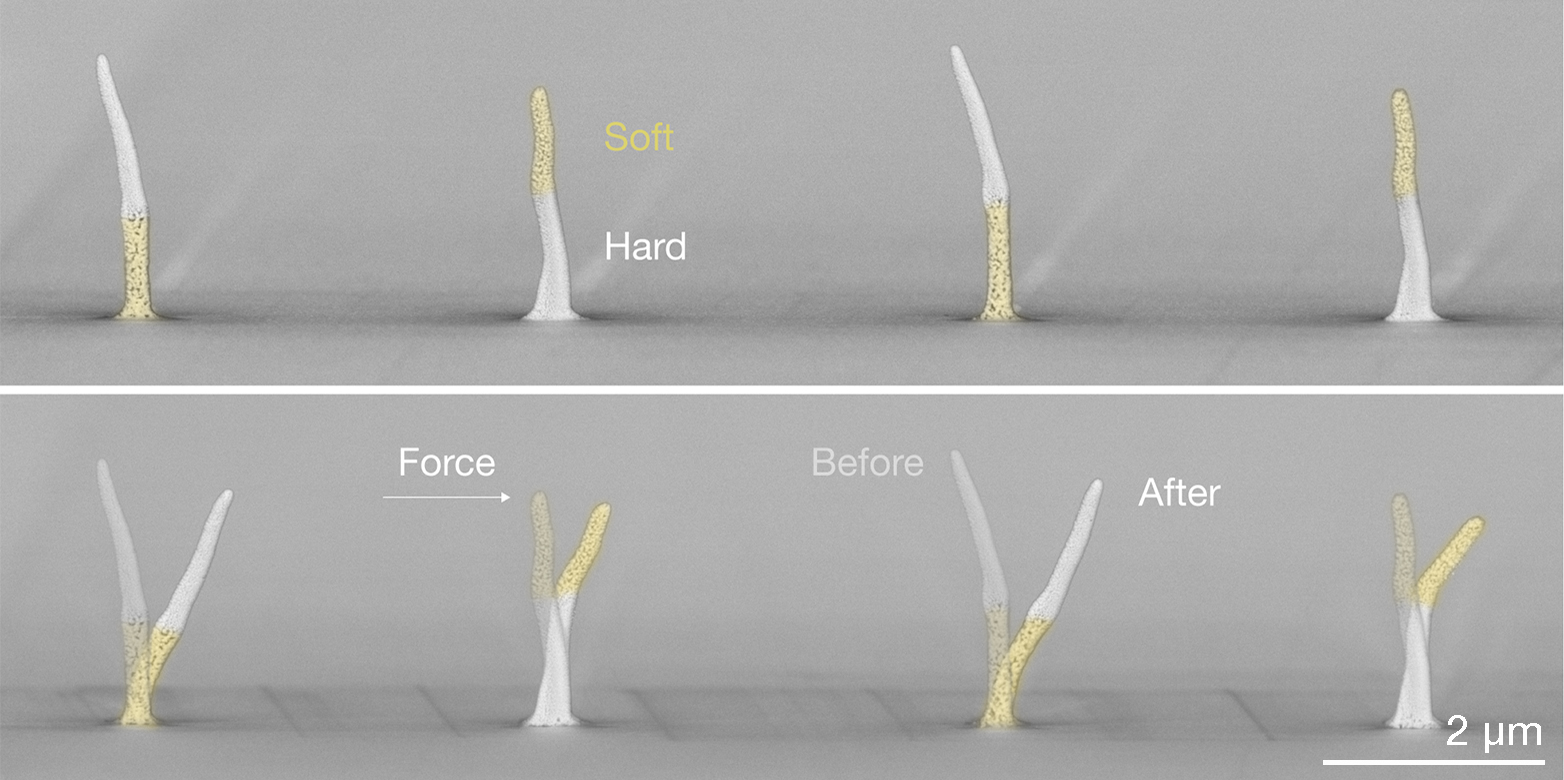
In the future, the researchers are planning to broaden the range of printable materials aiming to apply their technique for device fabrication, e.g. all-printed integrated circuits, sensor applications and optical metamaterials.
- ETH News: German, English
- Alain Reiser, Marcus Lindén, Patrik Rohner, Adrien Marchand, Henning Galinski, Alla S. Sologubenko, Jeffrey M. Wheeler, Renato Zenobi, Dimos Poulikakos & Ralph Spolenak: Multi-metal electrohydrodynamic redox 3D printing at the submicron scale. Nature Communications 10, 1853 (2019). external page DOI:10.1038/s41467-019-09827-1
The research was supported by grant No. ETH 47 14-2 and partially supported by grants No. SNF 200021-146180 and SNF 200020-178765.